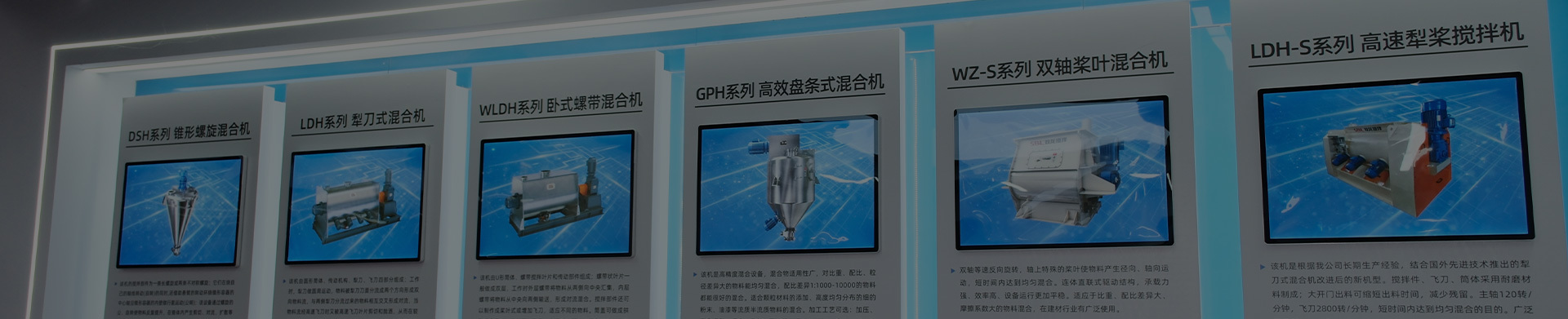
Product Name:
Conventional Jacket Mixer with ASME
Product Category:
Keyword:
Product Description
A jacketed mixing tank is a type of container used to circulate cooling or heating fluid around the outside of the tank in order to regulate the temperature within. When specifying the jacket there are many factors to take into consideration, including the heat transfer efficiency, weight, and adaptability of the heating or cooling requirements. The benefits of each jacket option for the vessel's overall performance and utility vary. Thus, making the choice a crucial step.
The jacket is a hollow on the exterior of the container that permits a uniform heat exchange between the walls and the fluid inside the container. Depending on the design, jackets come in several types.
▼ Some Typical Heating Cooling Jackets
▌Dryer Mixer with Conventional Jacket
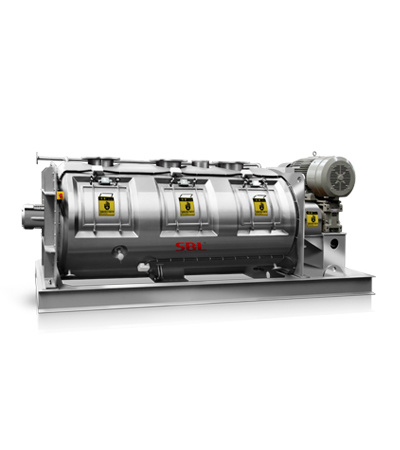
Conventional jacket is one of the most popular jackets for dryer mixer. That is a mixer with a second shell over the portion of the vessel. The cooling or heating medium flows run in the annular space including baffles internal.
With the development of material process, the mixer is more and more used for multi-functional mixing. The dryer mixer could be applied for mixing material with max 70% water content and dry it through heating jacket together with vacuum. For some particular material, the drying effect could be 0.05% water content at last. The basic design of dryer is a stationary horizontal cylinder, which is top loaded and bottom discharged. The standard tools are plow-shaped and radiate from a horizontal shaft that is supported by outboard bearings. Other mixing tool designs are also available.
This dryer operates according to the proven "fluidized bed" mixing principle whereby the materials being reacted are maintained in a mechanically fluidized suspended state, thus permitting the reacting mediums, gas-solid, or liquid-solid, to achieve intimate contact with each other and the heat transfer surfaces.
Heating jacket and vacuum design is needed. During mixing and drying process, the material will be dried through heating jacket transfer heat into vessel. Then, huge steam pressure will be happen inside vessel and take steam out by vacuum pump. According to different applications, different kind of mixer and mixing agitator could be used. We design dryer mixer comply with pressure vessel code to ensure safety use and quality.
Features
● Heavy duty design with adjustable shaft speed
● Horizontal or Conical Vessel Dryer
● Multiple heating medium
● Vacuum design for vessel
● High speed chopper for de-agglomeration requirement
● Jacketed Vessel with heating and cooling
Suitable Mixer Type
● Plough Mixer
● Twin Shafts Paddle Mixer
● Ribbon Mixer
Industries
● Denaturated starch
● Calcium soap
● Organic compounds
● Moisture Material
● Sludge
▌Dryer Mixer with Dimple Jacket
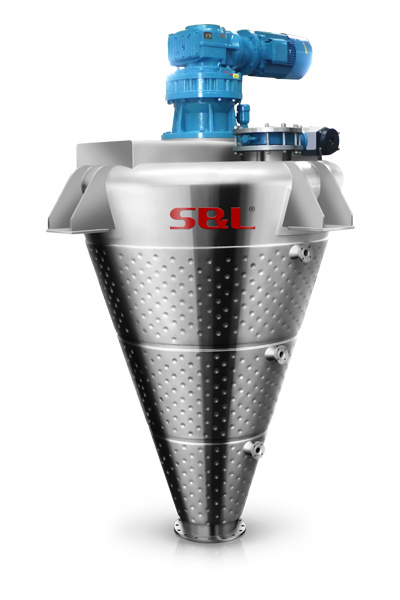
Dimple jacket is one of the most popular jackets for dryer mixer. That is a mixer with a thin external shell affixed to the vessel shell with spot welds onto the potions of the vessel. The cooling or heating medium flows through the jacket.
With the development of material process, the mixer is more and more used for multi-functional mixing. The dryer mixer could be applied for mixing material with max 70% water content and dry it through heating jacket together with vacuum. For some particular material, the drying effect could be 0.05% water content at last. The basic design of dryer is a stationary horizontal cylinder, which is top loaded and bottom discharged. The standard tools are plow-shaped and radiate from a horizontal shaft that is supported by outboard bearings. Other mixing tool designs are also available.
This dryer operates according to the proven "fluidized bed" mixing principle whereby the materials being reacted are maintained in a mechanically fluidized suspended state, thus permitting the reacting mediums, gas-solid, or liquid-solid, to achieve intimate contact with each other and the heat transfer surfaces.
Heating jacket and vacuum design is needed. During mixing and drying process, the material will be dried through heating jacket transfer heat into vessel. Then, huge steam pressure will be happen inside vessel and take steam out by vacuum pump. According to different applications, different kind of mixer and mixing agitator could be used. We design dryer mixer comply with pressure vessel code to ensure safety use and quality.
Features
● Heavy duty design with adjustable shaft speed
● Horizontal or Conical Vessel Dryer
● Multiple heating medium
● Vacuum design for vessel
● High speed chopper for de-agglomeration requirement
● Jacketed Vessel with heating and cooling
Suitable Mixer Type
● Plough Mixer
● Twin Shafts Paddle Mixer
● Ribbon Mixer
Industries
● Denaturated starch
● Calcium soap
● Organic compounds
● Moisture Material
● Sludge
Related Products
Different from traditional batch type mixer, continuous mixer provide a more economical alternation for big capacity to meet process requirement.
Continuous Mixer With Heating/Cooling Jacket
For a kind horizontal mixer, we can apply CIP to have perfect performance for hygienic production. Clean-in-Place-CIP system can be added for all our horizontal mixers.
Contact Us
We will contact you within one working day. Please pay attention to your email.
Industries